Echtzeit-Ortungssysteme (Real-Time Location Systems, RTLS) erfreuen sich zunehmender Beliebtheit bei Fertigungsunternehmen in verschiedenen Branchen. Sie werden hauptsächlich eingesetzt, um die Effizienz der Produktionsprozesse zu verbessern und die Ressourcen besser zu verteilen.
In den letzten Jahren hat der weltweite RTLS-Markt immer mehr an Bedeutung gewonnen (ein jährliches Wachstum von mehr als 17 % wird prognostiziert). Das liegt vor allem daran, dass immer mehr Unternehmen die Vorteile von Entscheidungen zur Optimierung von Produktionsprozessen erkennen, die auf realen Daten beruhen, die nicht nur von Maschinen geliefert werden, sondern - dank des Internets der Dinge - auch von mobilen Ressourcen gesammelt werden, die an Produktions- und internen Logistikprozessen beteiligt sind.
Das Anbringen eines Standort-Tags an einer solchen Ressource, wie z. B. einem Gabelstapler, ist eine sehr effektive Lösung zur Erfassung von Ineffizienzen bei der Nutzung. Ein noch größerer Nutzen lässt sich aus der Analyse der Bewegungen von Arbeitern ziehen, die in der Produktion eine wichtigere Rolle spielen als Gabelstapler. Auch wenn eine solche Maßnahme einige Bedenken aufwirft, hängt alles davon ab, für welche Zwecke der Arbeitgeber die erhobenen Daten verwenden will. Es ist wichtig, daran zu denken, dass sie jedoch durch das Arbeitsgesetzbuch und die Datenschutzbestimmungen eingeschränkt sind.
Unserer Erfahrung nach werden die Daten über die Bewegung und den Standort der Mitarbeiter in erster Linie dazu verwendet, die Effizienz des Produktionsprozesses zu analysieren und die Arbeitskosten automatisch zuzuordnen. In der Tat ist dies in der Regel nur eine Erweiterung der Arbeit, die die Lean- und Finanzabteilungen bereits leisten. Die Umsetzung von Schlussfolgerungen aus der Analyse von Standortdaten kann auch in Bereichen wie der internen Logistik und dem Lagermanagement viele Vorteile bringen, da viele dieser Prozesse trotz zunehmender Automatisierung hauptsächlich von Menschen durchgeführt werden.
In diesem Artikel erfahren Sie, wie ein Fertigungsunternehmen die Produktivität seiner Mitarbeiter mit einem Echtzeit-Ortungssystem verbessern kann.
Wie überwacht man die Bewegungen von Mitarbeitern in einer Produktionsanlage oder einem Lager?
Das Real Time Asset Location System, das auf Präzisionslösungen wie der Ultra Wideband (UWB)-Technologie basiert, verwendet diskrete Ortungsgeräte (Sender), die von den Mitarbeitern am Handgelenk, in der Tasche oder am Helm getragen werden. Sie können auch als Zugangskarten verwendet werden. Die Ortungsgeräte ermöglichen die Überwachung der Bewegung und des Standorts von Arbeitnehmern in Echtzeit, selbst in großen Industrieanlagen wie Lagerhäusern und Produktionsstätten. Die Ortungsgeräte senden Daten mit hoher Frequenz an Signalempfänger, die an der Decke oder an Pfeilern installiert sind. Diese übertragen die Daten in die Cloud, wo sie u. a. in Form von Wärmekarten zur Verfügung stehen.
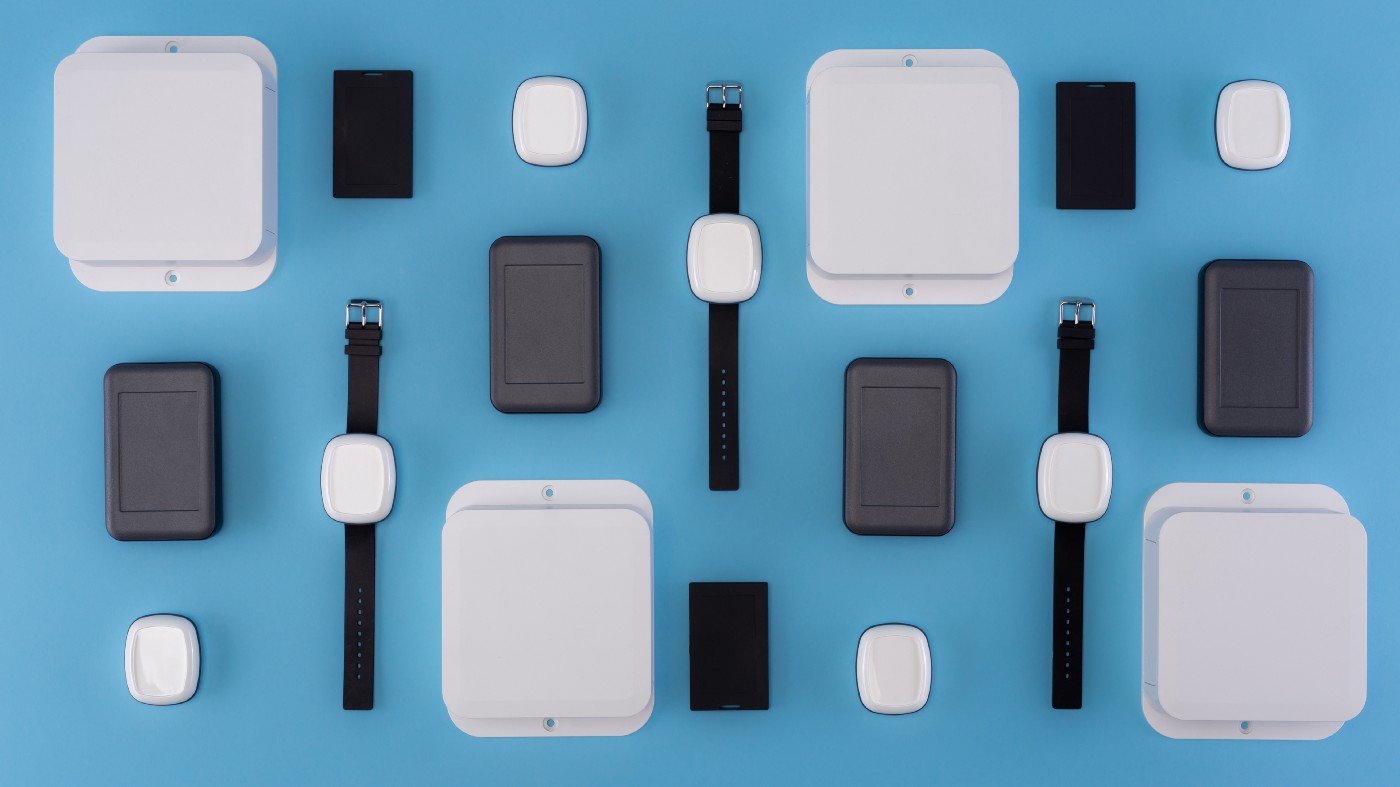
Wie lässt sich die Produktivität der Mitarbeiter mit einem Echtzeit-Ortungssystem verbessern?
Da man nichts verbessern kann, was nicht gemessen wird, ist der erste Schritt zur Produktivitätsverbesserung die Erfassung genauer Echtzeitdaten über die Prozesse, an denen die Mitarbeiter direkt beteiligt sind. RTLS-Systeme, wie z. B. Indoorway, können rund um die Uhr und ohne Unterbrechung arbeiten und Standortdaten mit einer Genauigkeit von weniger als einem Meter liefern. Die Daten werden dann je nach Bedarf in einer Vielzahl von Formaten visualisiert. Sie können sich beispielsweise auf die Aktivität (in Form von Heatmaps), die in verschiedenen Zonen verbrachte Zeit (jede Produktionsstätte kann eine eigene Zone sein), die Länge eines bestimmten Zyklus einschließlich Abweichungen usw. beziehen. Sie können diese Informationen dann zwischen Schichten, einzelnen Mitarbeitern (z. B. deren Dienstalter, um die Unterschiede zwischen erfahrenen und neuen Mitarbeitern zu sehen) oder in Bezug auf verschiedene Produkte vergleichen.
Die gewonnenen Informationen können auf verschiedene Weise genutzt werden:
1. Änderungen mit schnellen Ergebnissen (schnelle Erfolge)
Unsere Kunden sind immer wieder überrascht, wie viel sie schon wenige Tage nach Beginn der regelmäßigen Verkehrsmessungen über ihre Prozesse erfahren. Oft handelt es sich um offensichtliche Dinge, die bekannt waren, aber nur wenige haben das Ausmaß des Problems erkannt. Es gibt aber auch ganz unerwartete und nicht offensichtliche Entdeckungen.
Zu diesen Beobachtungen gehören beispielsweise Informationen über das Ausmaß der Unterschiede in den Arbeitsmethoden der verschiedenen Arbeitnehmer, die sich direkt auf ihre Produktivität auswirken. Eine angemessene Reaktion kann hier z. B. eine zusätzliche Schulung ausgewählter Mitarbeiter sein. Andere Quick Wins können z. B. geringfügige Änderungen in Bezug auf die Anordnung oder den Transport von Halbfertigprodukten, die Einführung einer besseren Kennzeichnung oder geringfügige Anpassungen der Verfahren betreffen. Der Initiator solcher Veränderungen ist in der Regel ein Lean Manager oder Schichtleiter.
2. Optimierung des Produktionsprozesses
Andere Änderungen, die auf der Grundlage von Informationen über den Standort und die Mobilität von Arbeitnehmern vorgenommen werden, erfordern in der Regel einen systematischeren Ansatz und tiefere Überlegungen.
Eine der häufigsten Anwendungen eines Systems wie Indoorway ist es, die Produktivität in verschiedenen Phasen des Produktionsprozesses zu verstehen. Anhand von Daten darüber, wie viele Arbeitnehmer wie lange an bestimmten Produktionsnestern beteiligt waren, und in Kenntnis des Zeitpunkts der Auftragsausführung können die Produktionsleiter und die Finanzabteilung diese Daten im Hinblick auf das produzierte Sortiment analysieren und auf dieser Grundlage die Arbeitsorganisation oder die Zuweisung von Ressourcen in weniger produktiven Phasen verbessern. Infolgedessen können die Kosten gesenkt werden, z. B. durch:
- Verringerung des Erwartungsabfalls durch Aufstockung des Personals an Stellen, an denen es aufgrund von Engpässen zu Problemen kommt,
- Verbesserung des Personaleinsatzes im Schichtbetrieb,
- Einführung der Automatisierung ausgewählter Phasen des Produktionsprozesses, z. B. durch die Anschaffung von FTS.???
3. Optimierung der Arbeitsabläufe
Laut der Zeitschrift Supply & Demand Chain Executive verschwendet der durchschnittliche Lagerarbeiter jährlich 6,9 Wochen mit unnötigen Bewegungen. Die Verluste durch unnötige Bewegungen der Mitarbeiter und unnötige Transporte in der Produktion sind ebenfalls hoch, und ihre Verringerung ist eine der Prioritäten der Methodik der schlanken Produktion. Leider ist die Verringerung dieser Verluste oft eine Herausforderung, da es bisher schwierig war, ihr Ausmaß und ihren Umfang zu messen. Spaghetti-Diagramme können für eine solche Anwendung nützlich sein, aber sie haben auch viele Einschränkungen - vor allem die begrenzte Beobachtungszeit und die Genauigkeit der handgezeichneten Linien, die gering ist und nicht mit der Welt der digitalen Daten übereinstimmt.
In diesem Fall ist ein System wie RTLS sehr nützlich, mit dem nicht nur genaue Spaghetti-Diagramme erstellt werden können, sondern auch sehr viel nützlichere Heatmaps, die die Bewegungen der am Produktions- und internen Logistikprozess beteiligten Mitarbeiter zeigen. Mit der Echtzeitlösung ist es beispielsweise möglich, den Aktivitätsgrad der Mitarbeiter zu ermitteln, indem berechnet wird, wie oft ein überwachter Mitarbeiter eine bestimmte Zone während einer Schicht betreten hat. Der Manager kann diese Daten dann in einem speziellen Analysebericht einsehen und daraus Schlüsse ziehen:
- die zeitaufwändigsten Aufgaben (ermittelt durch einen Vergleich des Aktivitätsniveaus der Mitarbeiter in den ausgewählten Zonen),
- Gründe für Produktivitätsunterschiede während einer Schicht und zwischen den Schichten (auf der Grundlage von Indikatoren für Verspätungen, ungleiche Arbeitsverteilung),
- Probleme, die zu Verzögerungen und unzureichender Leistung führen (zu wenig Personal für eine Schicht usw.).
Zusammenfassung
Der Hauptvorteil von RTLS gegenüber den derzeitigen Praktiken, die zur Prozessoptimierung führen, ist die Möglichkeit, Entscheidungen auf Zahlen und nicht nur auf Beobachtungen zu stützen. Dies macht es sehr einfach, Gespräche zwischen verschiedenen Abteilungen und Personen zu führen, insbesondere mit der für den Haushalt zuständigen Leitung. Sonst sagt der Chef am Ende: "Wenn wir Daten haben, sollten wir sie uns auch ansehen. Aber wenn wir nur Meinungen haben, sollten wir uns darauf einigen, dass ich immer Recht habe".
Möchten Sie mehr erfahren? Besuchen Sie die Indoorway-Lösungsseite und sehen Sie, wo die Technologie zur Lokalisierung von Anlagenbewegungen und zur Prozessüberwachung gut funktioniert, oder schreiben Sie uns eine E-Mail an indoorway@aiut.com.