Systemy pomiaru lokalizacji zasobów w czasie rzeczywistym (RTLS — ang. Real-Time Location System) stają się coraz częściej używanym rozwiązaniem przez firmy produkcyjne z różnych branż. Są stosowane głównie do poprawy efektywności procesów produkcji oraz lepszej alokacji zasobów.
W ostatnich latach globalny rynek RTLS zyskuje na znaczeniu (przewiduje się jego wzrost o ponad 17% rocznie). Wynika to głównie z faktu, że coraz więcej firm zdaje sobie sprawę z zalet podejmowania decyzji o optymalizacji procesów produkcji w oparciu o rzeczywiste dane dostarczane nie tylko przez maszyny, ale też — dzięki Internetowi Rzeczy — zbierane z ruchomych zasobów zaangażowanych w procesy produkcji i logistyki wewnętrznej.
Przymocowanie taga lokalizacyjnego do takiego zasobu, np. wózka widłowego, jest bardzo skutecznym rozwiązaniem pozwalającym na wychwycenie nieefektywności jego użycia. Jeszcze większe korzyści można uzyskać na podstawie analizy ruchu pracowników, którzy odgrywają bardziej znaczącą rolę w produkcji niż wózki. Chociaż takie działanie może budzić pewne obawy, wszystko zależy od celów, do jakich pracodawca chce użyć zbieranych danych. Należy pamiętać, że są oni jednak ograniczeni kodeksem pracy, a także regulacjami o ochronie danych osobowych.
Z naszego doświadczenia wynika, że, dane o ruchu i lokalizacji pracowników służą przede wszystkim do analizy wydajności procesu produkcji oraz automatycznej alokacji kosztów pracy. Jest to zresztą zazwyczaj tylko rozszerzenie pracy, jaką robią już komórki Lean oraz działy finansowe. Wdrożenie wniosków z analizy danych lokalizacyjnych może też dostarczyć wiele korzyści w obszarach takich jak logistyka wewnętrzna i gospodarka magazynowa, ponieważ wiele z tych procesów, mimo postępującej automatyzacji, jest obsługiwanych głównie przez ludzi.
W tym artykule omawiamy sposoby, w jakie firma produkcyjna może poprawić produktywność pracowników dzięki systemowi lokalizacji w czasie rzeczywistym.
Jak monitorować ruch pracowników w zakładzie produkcyjnym lub magazynie?
System Lokalizacji Zasobów w Czasie Rzeczywistym oparty na precyzyjnych rozwiązaniach, takich jak technologia Ultra Wideband (UWB), wykorzystuje dyskretne lokalizatory (nadajniki), noszone przez pracowników na nadgarstku, w kieszeni, lub na kasku. Mogą być też używane jako karty dostępu. Lokalizatory umożliwiają monitoring ruchu i lokalizacji pracowników w czasie rzeczywistym nawet w rozległych przestrzeniach przemysłowych, takich jak magazyny i zakłady produkcyjne. Lokalizatory przesyłają dane z dużą częstotliwością do odbiorników sygnału zainstalowanych na suficie lub filarach, które następnie przesyłają je do chmury, gdzie są dostępne w postaci m.in. map ciepła.
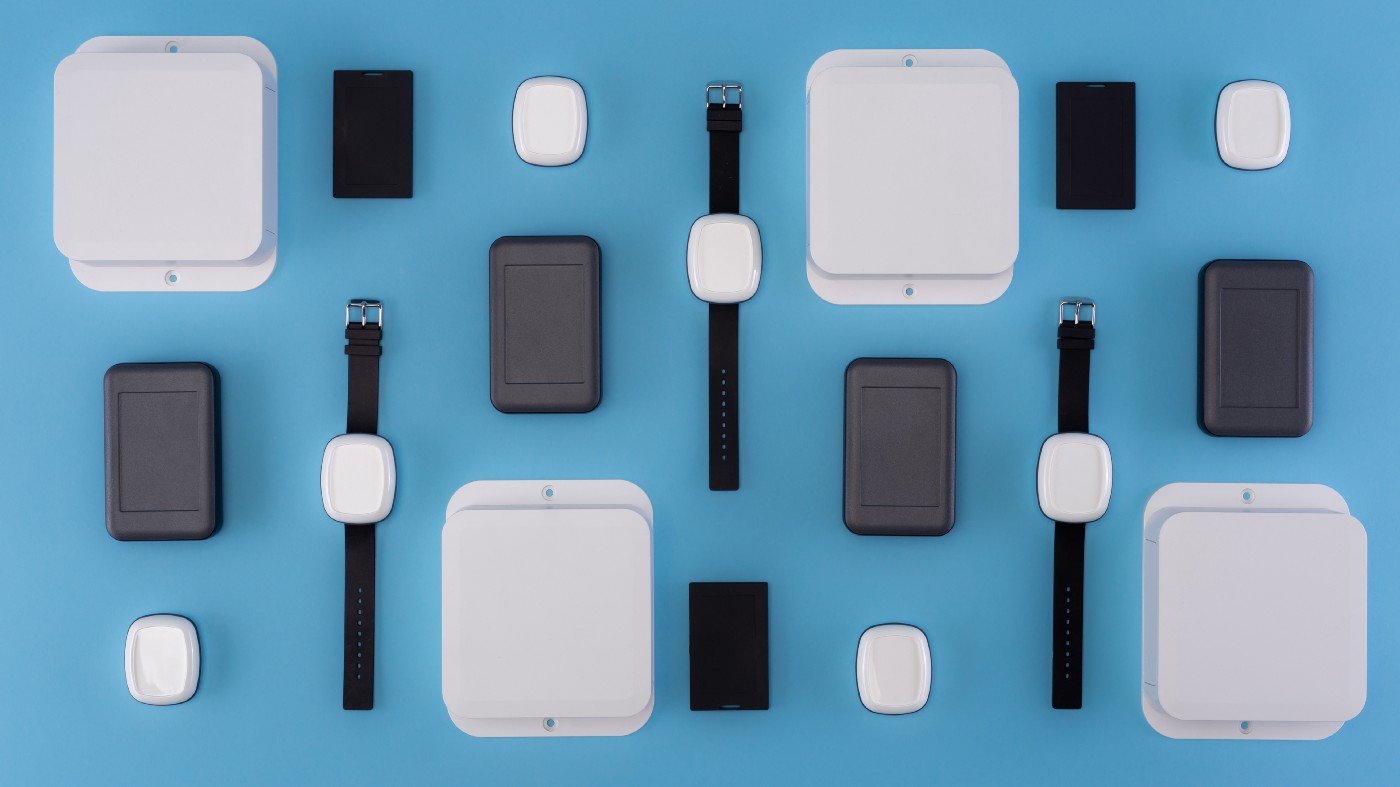
Jak poprawić produktywność pracowników za pomocą systemu lokalizacji w czasie rzeczywistym?
Ponieważ nie można poprawić czegoś, co nie jest mierzone, pierwszym krokiem do poprawy produktywności są dokładne i rzeczywiste dane o przebiegu procesów, w które bezpośrednio zaangażowani są pracownicy. Systemy RTLS, takie jak Indoorway, mogą działać bez przerw przez całą dobę i są w stanie dostarczyć dane o lokalizacji z dokładnością poniżej jednego metra. Dane są następnie wizualizowane w różnych formatach, w zależności od potrzeb. Mogą dotyczyć na przykład aktywności (w postaci map ciepła), ilości czasu spędzonej w różnych strefach (każde gniazdo produkcyjne może być osobną strefą), długości danego cyklu wraz z odchyleniami, itp. Następnie można porównać te informacje między zmianami, poszczególnymi pracownikami (np. ich stażem, żeby zobaczyć różnice pomiędzy doświadczonymi a nowymi pracownikami) lub pod kątem różnych produktów.
Uzyskane informacje można wykorzystać na kilka różnych sposobów:
1. Zmiany dające szybkie efekty (quick wins)
Nasi klienci są niezmiennie zdziwieni, jak wiele dowiadują się o swoich procesach już po kilku dniach od rozpoczęcia regularnych pomiarów ruchu. Często są to rzeczy oczywiste, o których było wiadomo, ale mało kto zdawał sobie sprawę ze skali problemu. Zdarzają się jednak też dość niespodziewane i nieoczywiste odkrycia.
Wśród takich obserwacji znajdują się np. informacje o skali różnic w sposobie pracy pomiędzy różnymi pracownikami, co przekłada się bezpośrednio na ich produktywność. Tutaj odpowiednią reakcją może być np. dodatkowe szkolenie wybranych pracowników. Inne quick wins mogą dotyczyć np. drobnych zmian związanych z ułożeniem lub transportem półproduktów, wprowadzenie lepszego oznakowania czy też niewielkie korekty procedur. Inicjatorem tego typu zmian jest zazwyczaj lean manager lub kierownik zmiany.
2. Optymalizacja procesu produkcji
Pozostałe zmiany dokonywane na podstawie informacji o lokalizacji i ruchu pracowników wymagają już zazwyczaj bardziej systemowego podejścia i głębszego namysłu.
Jednym z najczęstszych zastosowań takiego systemu jak Indoorway jest zrozumienie produktywności na poszczególnych etapach procesu produkcji. Mając dane o tym ilu pracowników i jak długo było zaangażowanych na poszczególnych gniazdach produkcyjnych oraz znając czas realizacji zleceń , kierownicy produkcji oraz dział finansowy mogą przeanalizować te dane pod kątem produkowanego asortymentu i na tej podstawie poprawić organizację pracy lub alokację zasobów na etapach, które są mniej wydajne. W efekcie można zmniejszyć koszty np. poprzez:
- ograniczenie straty Oczekiwania, dzięki zwiększeniu ilości pracowników w miejscach, gdzie z powodów niedoborów powstają wąskie gardła,
- poprawienie alokacji pracowników na poszczególnych zmianach,
- wprowadzenie automatyzacji wybranych etapów procesu produkcji np. poprzez zakup AGV.
3. Optymalizacja sposobu pracy
Według magazynu Supply & Demand Chain Executive przeciętny pracownik magazynu marnuje rocznie 6,9 tygodnia na niepotrzebny ruch. Straty wynikające ze zbędnego ruchu pracowników oraz niepotrzebnego transportu na produkcji są również wysokie, a ich ograniczenie jest jednym z priorytetów metodologii lean manufacturing. Niestety, ograniczenie tych strat jest często wyzwaniem, ponieważ do tej pory trudno było zmierzyć ich zakres i skalę. Diagramy spaghetti mogą być do takiego zastosowania przydatne, ale mają też dużo ograniczeń — przede wszystkim limitowany czas obserwacji oraz dokładność rysowanych ręcznie linii, która jest niska i nie pasuje do świata cyfrowych danych.
W takim przypadku bardzo przydaje się system typu RTLS, dzięki któremu można wygenerować nie tylko dokładne diagramy spaghetti, ale też dużo bardziej przydatne mapy ciepła pokazujące ruch pracowników zaangażowanych w proces produkcji i logistyki wewnętrznej. Korzystając z rozwiązania w czasie rzeczywistym, można np. określać poziomy aktywności pracowników, obliczając liczbę przypadków, w których monitorowany pracownik wchodził do określonej strefy podczas zmiany. Kierownik może następnie przejrzeć te dane w dedykowanym raporcie analitycznym i na ich podstawie zidentyfikować:
- najbardziej czasochłonne zadania (zidentyfikowane poprzez porównanie poziomów aktywności pracowników w wybranych strefach),
- przyczyny różnej wydajności podczas zmiany i między zmianami (na bazie wskaźników pokazujących opóźnienia, nierównomierny rozkład pracy),
- problemy prowadzące do opóźnień i gorszych wyników (niewystarczająca liczba pracowników pracujących na jednej zmianie itp.).
Podsumowanie
Główną przewagą RTLS nad obecnie stosowanymi praktykami prowadzącymi do optymalizacji procesów jest możliwość oparcia decyzji na liczbach, a nie jedynie obserwacjach. To bardzo ułatwia rozmowy między różnymi działami i osobami, a szczególnie z kierownictwem odpowiedzialnym za budżety. W przeciwnym razie kończy się tak, że szef mówi: “Jeśli mamy dane, popatrzmy na dane. Jeśli mamy jednak tylko opinie, umówmy się, że to ja mam zawsze rację”.
Chcesz dowiedzieć się więcej? Odwiedź stronę rozwiązania Indoorway i zobacz, w jakich obszarach sprawdza się technologia do lokalizacji ruchu zasobów i monitoringu procesów lub napisz do nas na indoorway@aiut.com