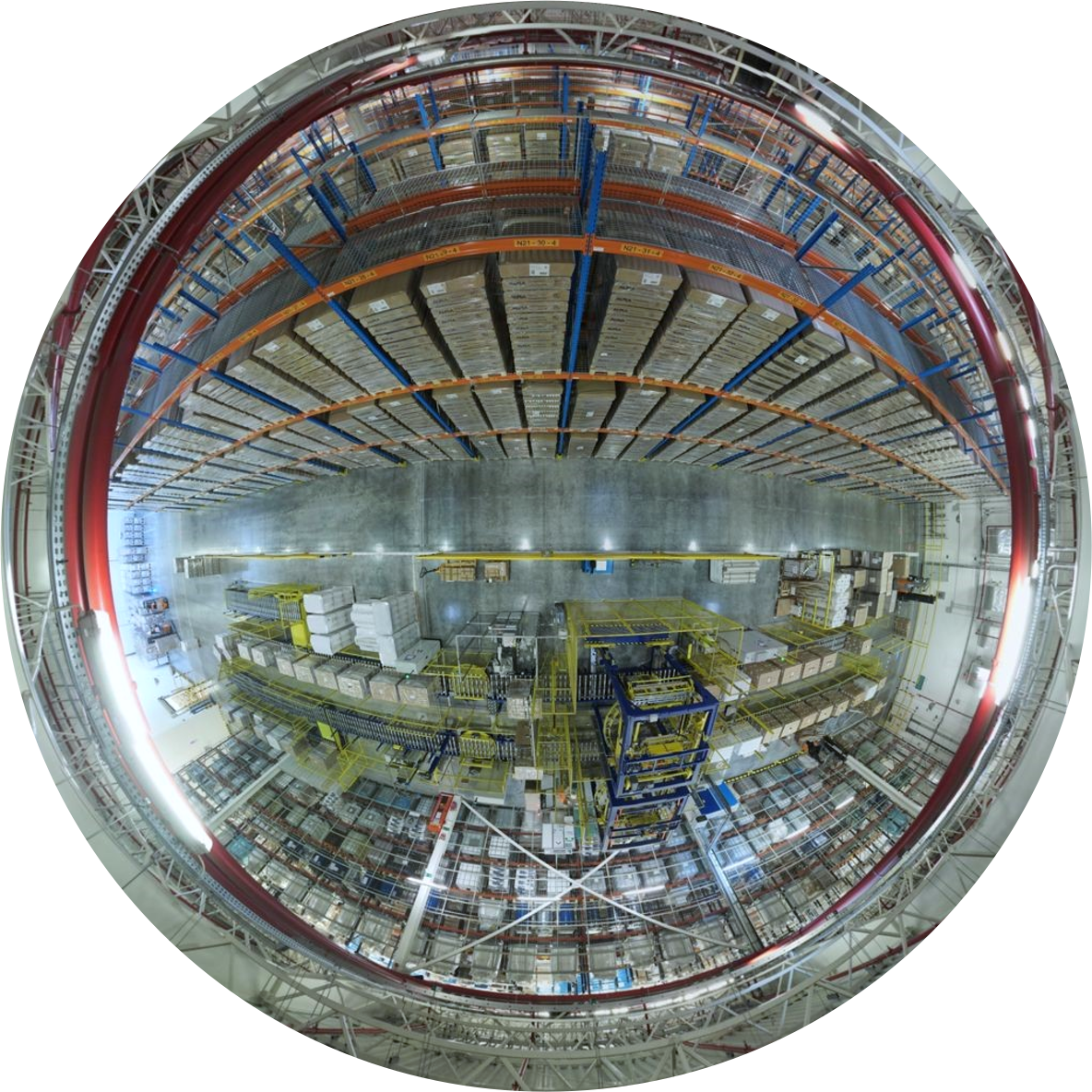
Improving warehouse efficiency
A case study of the Indoorway solution based on an implementation at the plant of cosmetics manufacturer L'Oreal near Warsaw.
A case study of the Indoorway solution based on an implementation at the plant of cosmetics manufacturer L'Oreal near Warsaw.
L'Oréal is a leading cosmetics manufacturer that has been present on the market since 1992. Its mission is to provide consumers around the world with innovative cosmetic products that are tested for quality, efficacy and safety.
„The data obtained from Indoorway enables us to make accurate decisions faster, minimizing the risk of mistakes. They are a reliable source of information and the only way to get a real picture of the situation in the factory. Moreover, data make it easier to find bottlenecks and allow us to define appropriate actions. An important value for me from the Indoorway solution was also the ability to involve employees in actions, that is, based on data, to make changes and set common standards that everyone can sign up to."
Łukasz Chochel, Warehouse Manager at L'Oréal Warsaw Plant