The customer noticed a serious problem in the operation of mobile robots (AGV/AMR), which were not systematically delivering raw materials to production. The mobile robots were able to hang up for long periods of time, blocking travel on communication routes. One of the robots was able to block the work of three others, which significantly reduced production efficiency and the amount of finished product produced. Manual monitoring was difficult because the area requiring monitoring was about 22 000 m². A solution was therefore needed that would immediately and automatically notify the maintenance team of unplanned stops.
.jpeg)
.jpeg)
By analyzing heat maps and spaghetti diagrams, we have identified areas with high mobile robots (AGV/AMR) traffic.
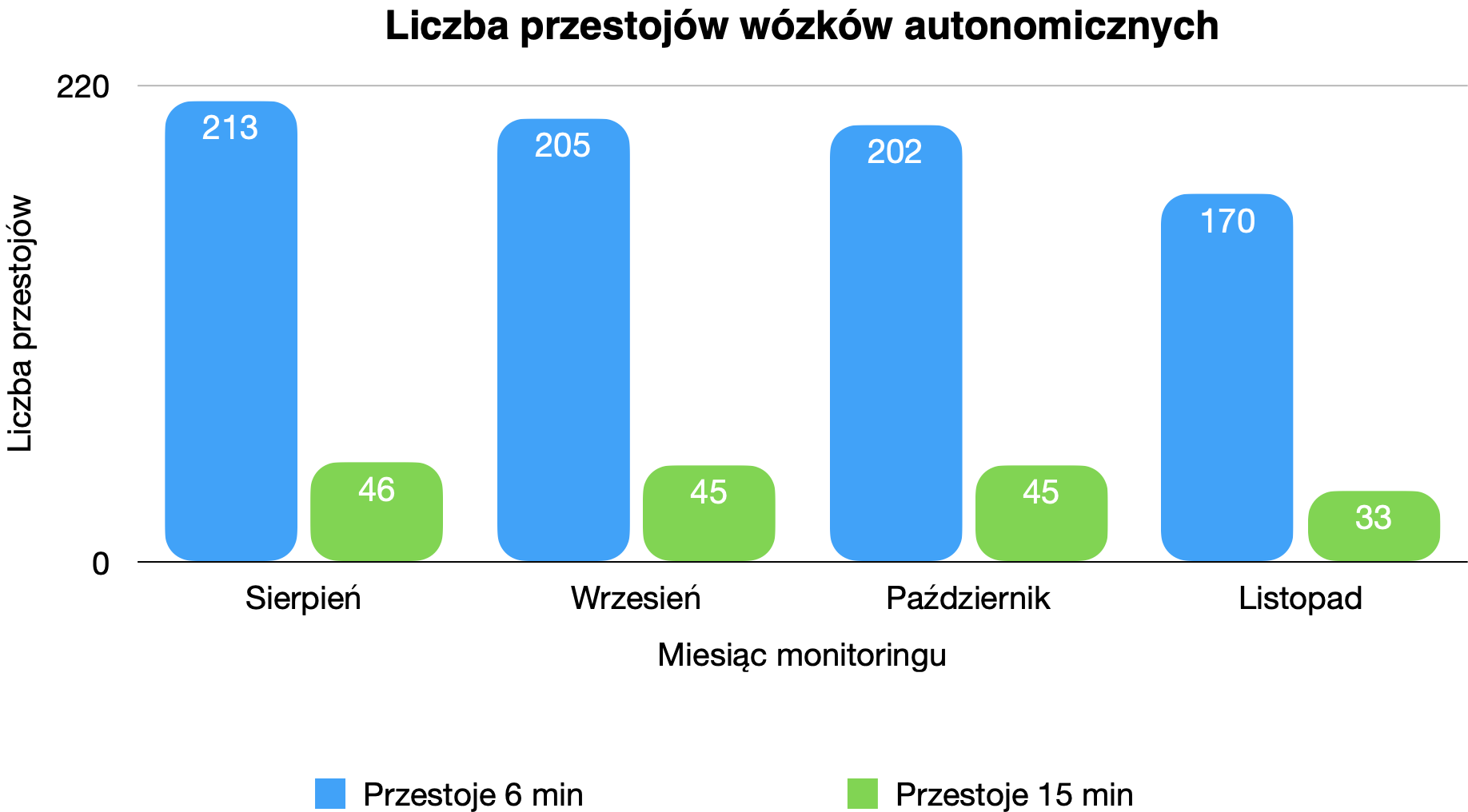
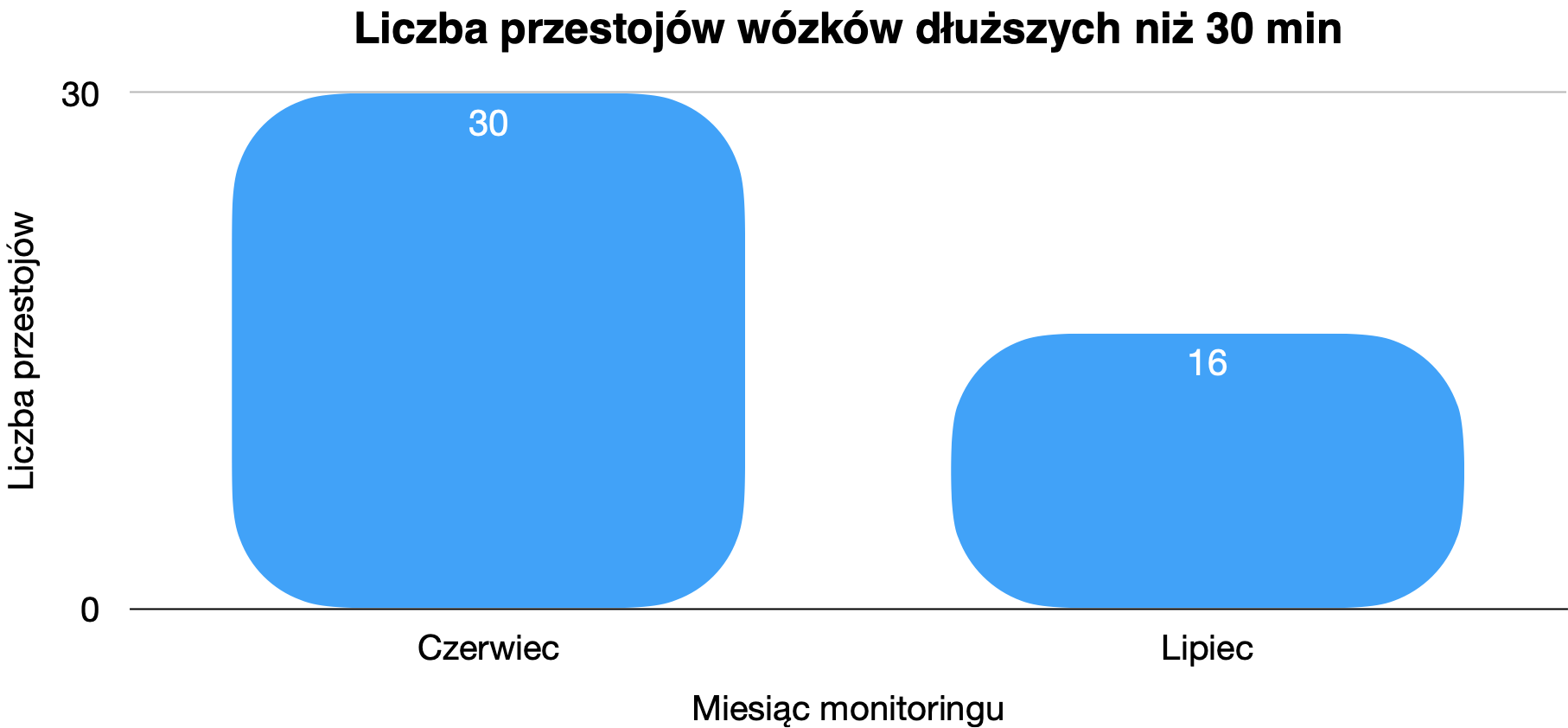
The data from the Indoorway system not only made it possible to accurately identify the problem and make improvements, but also to implement comprehensive changes improving the competence of warehouse and production employees.
The main activities included:
- Training for the factory crew, to refine training in resetting mobile robots (AGV/AMR). This enabled virtually every warehouse worker to get a mobile robot back on line, rather than just a few people.
- A notification system for unscheduled standstills of mobile robots (AGV/AMR) was set up, which monitored a very large area of mobile robots traffic, allowing maintenance workers to respond instantly to the alerts they received.
- The implemented changes helped reduce the number of long stoppages by 48% in just the second month of operation, affecting the delivery of raw materials on time to the production line.
- The first effects were visible as early as 8 weeks after the implementation of the system and the system monitored on an ongoing basis whether the introduced benefits were sustained over time and how they were affected by newly introduced changes in the production process.
Request a free call with a process optimization expert. We will check where the problem lies and offer a solution.
Requests a phone call